Lack of space was quite apparent so a plan had to be put in place. The car shops were occupying valuable land and would have to be relocated. It was decided to install a new spur for the car shops next to the two stall engine shed. Existing scenery was removed and the concrete floor pad was poured at the new location seen in the picture to the right of the engine house foundation.
Changing Times
After many years of operation with small locomotives, the D&RGW acquired a K-36 Class 2-8-2. The common practice of running the C-16 Class 2-8-0’s in reverse when returning from Sonjora to Rio Yard was not an option that could be applied to the K-36 Class loco. The time had come to expropriate some real estate and construct a turntable for Rio Yard.
Relocating the Car Shops
The New Plan
To make room for the new turntable, it was obvious that the existing tabletop was not large enough. The end of the tabletop had to be extended but that would be at the expense of aisle space. A few years ago, the entrance into the main layout area was widened in anticipation of an extension for a turntable. By sinking half of the new turntable into the existing bench work, a 12″ addition was all that was needed to accomodate the turntable.
Turntable
MDF (medium density fibreboard) was chosen for use in fabrication of the pit. MDF is more stable than plywood and would retain it’s dimensions with the changes in temperature and humidity in the train room. The only concern was to prevent water soaking into the MDF during scenicing and plaster operations. In my case, a good friend facilitated having the MDF laminated and cut on a CNC machine which made for a dimensionally perfect pit assembly. One could easily use a router with a circle cutter, band saw or sabre saw to cut the circles out of the MDF material.
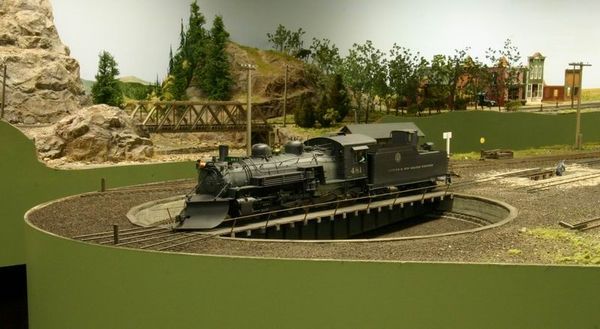
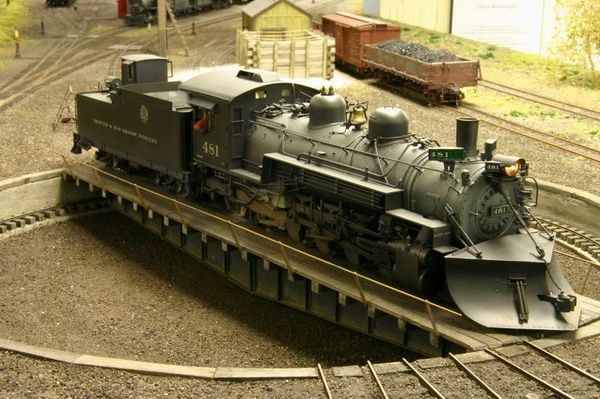
Drive Mechanism and Powering
The turntable is driven with a Switchmaster motor and rubber capstan against a 12″ diameter particle board disk. The Switchmaster is run through a Digitrax decoder so any throttle can operate the turntable without having to go to a control panel and turn a rheostat.
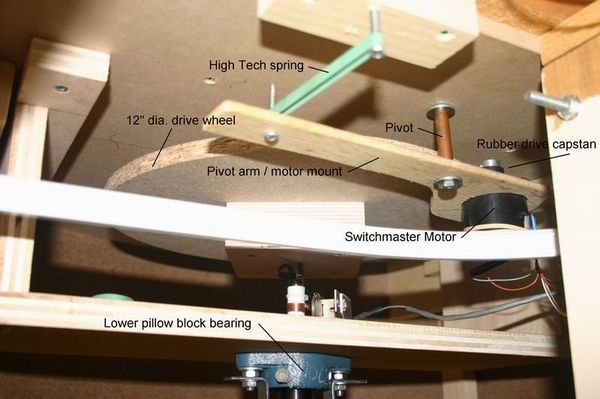
I used the keyway in the shaft to run two wires down to a pair of slip rings which can barely be seen in the picture of the drive parts. Two rings were cut from 1/2″ copper water pipe and insulated from the main shaft. Wipers were added to run on the rings. Being as my layout is DCC, I ran the power feed wires through an auto-reversing circuit. It would be a little easier to connect one rail to the shaft and the other to the pit rail. A simple wiper on the shaft would suffice and no insulating of the slip rings would be necessary.
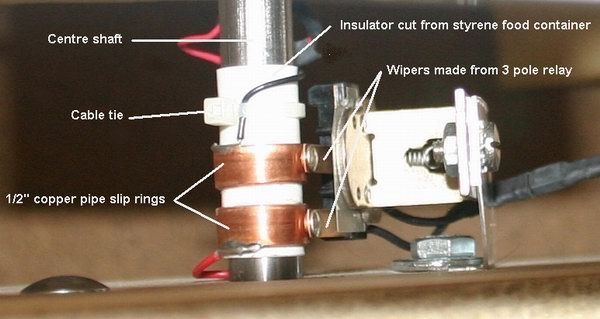